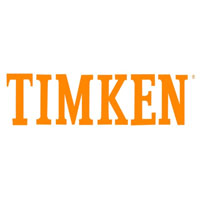
Profile / Bio-sketch:
Sanjay Koul is the Chairman and Managing Director of all operations in India for The Timken Company. He has responsibility for business and manufacturing operations, financial performance, and acceleration of growth in the markets in India. He was named Managing Director in October 2012 and took over as Chairman in August 2014. In November 2022, he was promoted as President of all operations of The Timken Company for India and South-East Asia.
Sanjay Koul joined Timken in 1990 as a Production Engineer and was among the first set of employees of the company who relocated to Jharkhand. Since then, he has served in additional positions within the rail and supply chain & Sales organizations. In 2007, he was named general manager of the Jamshedpur Plant. Two years later, he was named general manager of supply chain operations in Asia working out of Wuxi, and in 2011, he was named Director of manufacturing and supply chain management for Asia.
Sanjay holds a bachelor’s degree in mechanical engineering from the Birla Institute of Technology and Science and a master’s degree in business management from Xavier Labour Relations Institute. He completed the EDGE executive development program for senior Timken leaders at the University of Virginia Darden School of Business in 2008. He was conferred with honorary PhD this year by CIAC in collaboration with University of South Korea. He sits on the Executive Committee of AMCHAM India and on the Board of ELCIA apart from being involved with the manufacturing committee of CII.
Professional Achievements:
Sanjay’s promotion to President of all operations of The Timken Company for India and South-East Asia in November 2022 is a testament to his leadership & entrepreneurial abilities. Sanjay has amassed several awards and accolades over the past decade leading Timken. In recent years, some of his achievements include – recognized as one of the Best CEOs of 2022 by Fortune India, Business Icons of the year 2022 by Team Marksmen, Most Promising Business Leader of Asia by The Economic Times, and Best CEOs Award by Business Today among others.
An overview of your company: (Describe its niche, standing, products & services, Infrastructure & major strengths)
Timken engineers, manufactures, and markets bearings, gear drives, belts, chain, couplings, lubrication systems and related products, and offers a spectrum of powertrain rebuild and repair services. Timken applies its deep knowledge of metallurgy, tribology, and mechanical power transmission across a variety of bearings and related systems to improve reliability and efficiency of machinery and equipment around the world.
Timken started its India operations in 1989 and set up its first state-of-the-art manufacturing facility in Jamshedpur in 1992. Timken subsequently set up a manufacturing facility in Chennai in 2008. Further expanding its business in India, Timken acquired ABC Bearings in 2018.
Timken businesses in India are headquartered in Bangalore, which is also a Technology Centre, providing its customers a unique opportunity to access global pool of engineering expertise and the latest technological advancements.
Any turnaround story to narrate?
Leading Timken from a turnover of INR 694 Cr. in FY 2012-13 to INR to 2200 Cr. in 2021-22 by instilling value selling with focus on quality, agility and speed to market. The market cap grew from almost minimal to USD 2.5 BIL in last few years.
Have you embraced Industry 4.0 in your manufacturing as a long-term business strategy?
Timken introduced ‘Just in Time’ (JIT) and SPC in its manufacturing processes in late 80’s which became the norm years later. We were always ahead of the curve in introducing new technologies & innovations in making our manufacturing more efficient. We run our manufacturing using a concept called KBE (Knowledge Based Engineering) which consist of automation, digitization and everything that Industry 4.0 is all about. So, we were doing this much before everyone else.
Any digital transformation drives undertaken to improve quality and bring out better products through green manufacturing, with gains of cost-effectiveness:
We use Knowledge Based Engineering, process automation, digitization and several continuous improvement initiatives to improve the quality of our products as well as to streamline the manufacturing processes. We have sensor and camera-based systems for quality control. When you walk into our plants, we can show you digitally ‘Plan for Every Part’ (PFEP) and I can watch the plant from any corner of the world using BI. Our Manufacturing Technology team continuously works on new ways to improving the efficiency of our manufacturing processes. We don’t only follow LEAN as a practice; we’ve made it a way of life at our plants. We use renewable energy to run our plants. For example, 70% of the total energy used by our Chennai plant last year was solar and wind energy.
Exemplary R & D initiatives and technological breakthroughs, if any:
Timken is known as a leader in friction management around the world. We have a large, global pool of engineers working on making breakthroughs in this area, be it alternate materials, better machining, profiles which justify the load transfers, or material sciences. For example, the fastest trains in India – Vande Bharat (Train 18) runs on Timken bearings. Our R&D centre in Bangalore is one of the six in the world working every day to innovate new technologies to keep the world in motion.
A word about your leadership and operations management to achieve manufacturing excellence:
We have a comprehensive approach for achieving and sustaining excellence—from board room strategy to shop floor execution. We make sure that it Integrates strategy and leadership development. It carves a path for culture change that prepares hourly employees to take control of their processes and prepares management to enable them to do it. It also details an audit process for identifying priorities for improvement and tracking progress and ensuring sustainability
Efforts of import substitution to make India self-reliant (atmanirbhar):
Spherical Roller Bearings (SRB) and Cylindrical Roller Bearing (CRB) are used in several applications across different industries and come in varying sizes based on the application. We were making some of these in small numbers in Chennai and importing the rest from other Timken plants. However, looking at the growing demand, we are investing is a new manufacturing plant in Bharuch, Gujarat to make these products in India. We are exporting more and more of Made in India products to every part of the world. However, importing bearing cannot be wished away as there are millions of different part numbers, and everything cannot be produced in one country. Our focus is export more and more and we have received several awards for export promotion.